Blog
The benefits of automatic bale dewiring in the paper recycling industry
The benefits of automatic bale dewiring in the paper recycling industry
Paper and cardboard are among the most recycled materials in Western countries, and in the future, we can only expect the recycling rate to increase.
A high-performing paper recycling process, starting from material feeding, is a crucial factor when there is a need to keep recycling rates high. Not only does this serve factories, but also the environment.
When speaking of efficient recycling processes, the standards of the 2020s should rely on a high level of automation as well as traditional paper recycling.
Read this blog and learn more about how automatic bale dewiring can help your facility to save the environment, money, and people while the recycling process flows effectively.
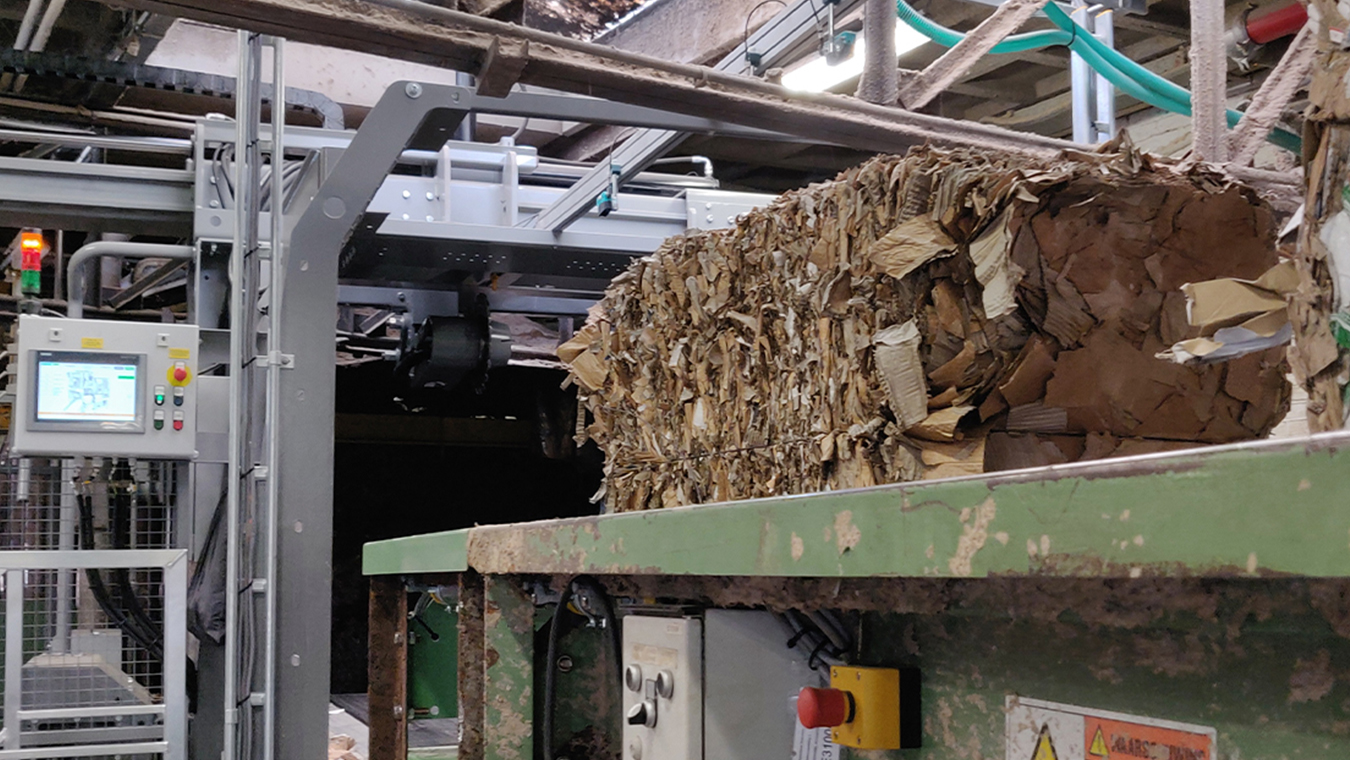
Reduce the need for landfill by minimizing ragging and reject in a new way
Recycling should not create more waste but reduce it. This is why one of the most important benefits of automation is the reduction and prevention of residue from paper recycling.
Ragger wire, or ragger rope or pulper tails, is a waste product born in paper recycling. Paper bales often contain impurities in addition to paper materials. When the contents of the bale enter the pulping process, the other material forms a mass in the pulper with water. For example, small plastic, metal parts and non-soluble paper form a ragger wire mass.
Steel wires from the paper bales are combined with the ragger rope pulp. In the pulping process, they form a non-recyclable mass because these materials are quite impossible to separate effectively. Thus ragger ropes must be landfilled, which creates landfilling costs and a huge cumulative amount of emissions.
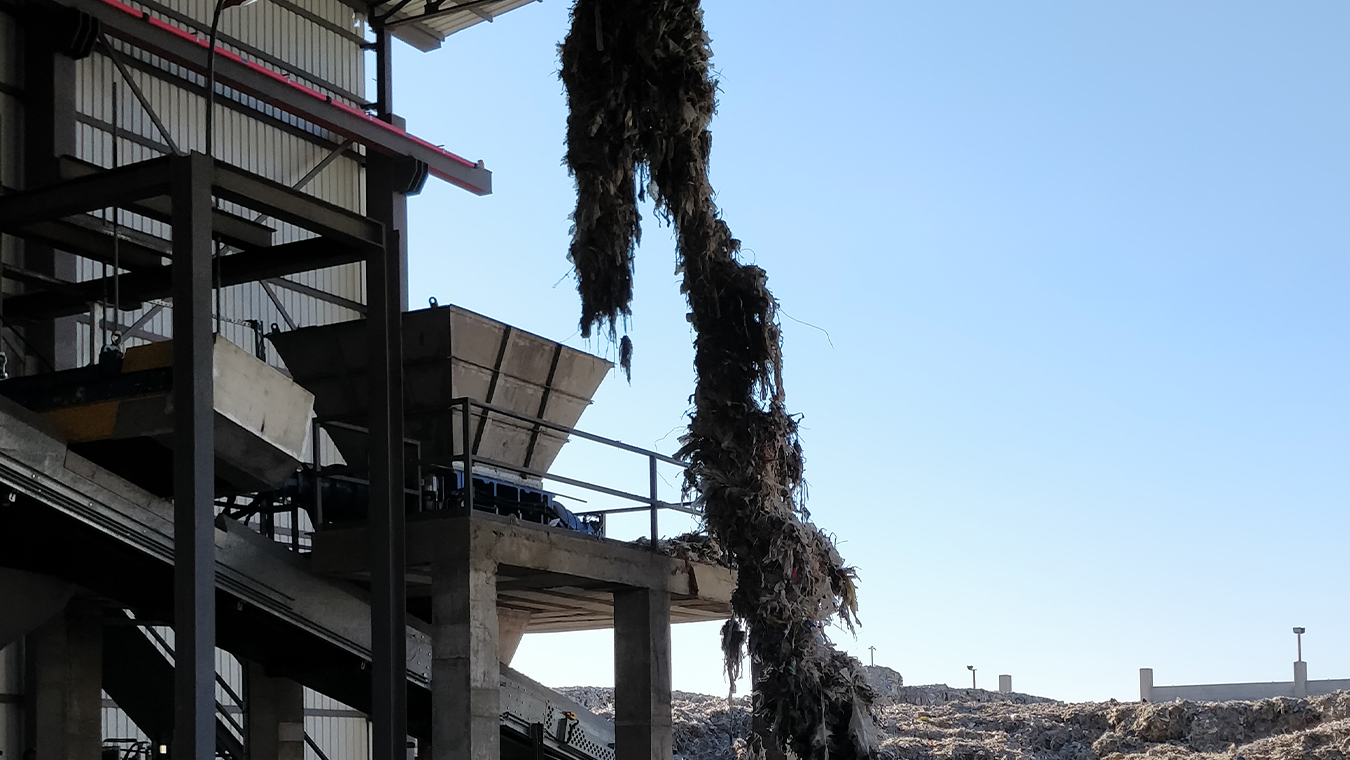
But what if you could prevent the formation of ragger rope in the first place? In that case, you would not have to deal with excessive amounts of rejects and you could reduce the need and costs of landfills – and work towards zero landfill goals. The purpose of the recycling process is to prolong the life of the material, but it is also logical to reduce residue from the recycling process.
Fully automated Cross Wrap Dewiring Machine presents a totally new way to reduce the amount of reject waste. It prevents unnecessary waste because instead of a traditional bale opening, it removes the wires from the material stream completely.
CW Dewiring Machine cuts the wires from individual paper bales before the pulping process. Then, the machine separates and coils the metal wires into clean bundles for easy recycling. This is notable as the metal has a very long lifespan if recycled correctly instead of being landfilled as a part of ragger rope.
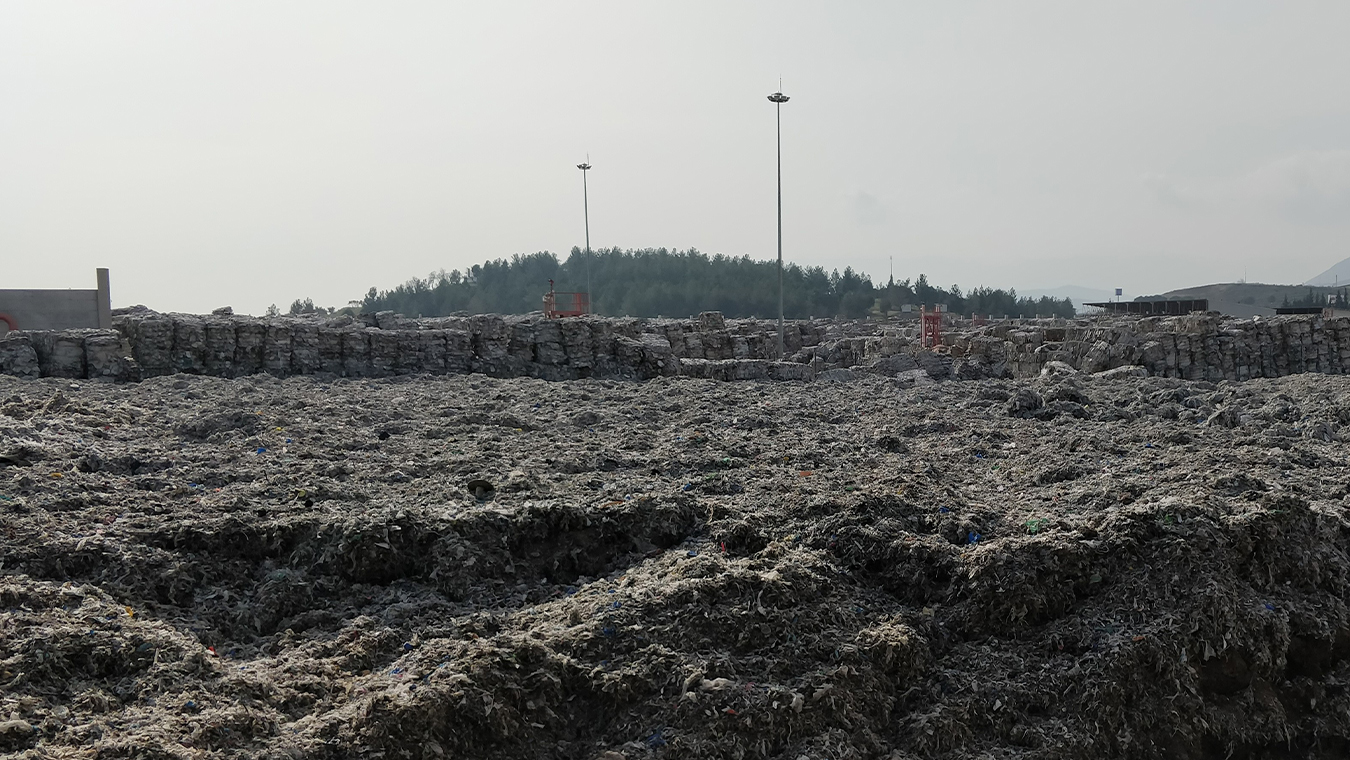
Read also: Make profit from reject and stop landfilling
Automation helps to remove costly and dangerous manual work
It is sometimes surprising that paper recycling processes are usually ultra-modern, automatised and effective, but one stage is sometimes neglected: the feeding of the material. The dewiring of paper bales with manual tools is always inefficient compared to the work of a machine with an automated and risk-free process.
If wires are not removed efficiently, it is just as harmful because then the wires become part of the material flow and ragger rope mass in the pulper.
Automation does not cancel out the need for human labor but directs the working hours towards safer and genuinely productive tasks. If you can offer your employees appealing and varying tasks, they are more dedicated to their work, too.
CW Dewiring Machine is also more reliable than manual work, as it keeps a steady pace 24/7 without rising costs. If you want to increase manual feeding, you need to increase shifts – and labor costs.
So the machine is constantly paying itself back, independent from the flow of material through the machine.
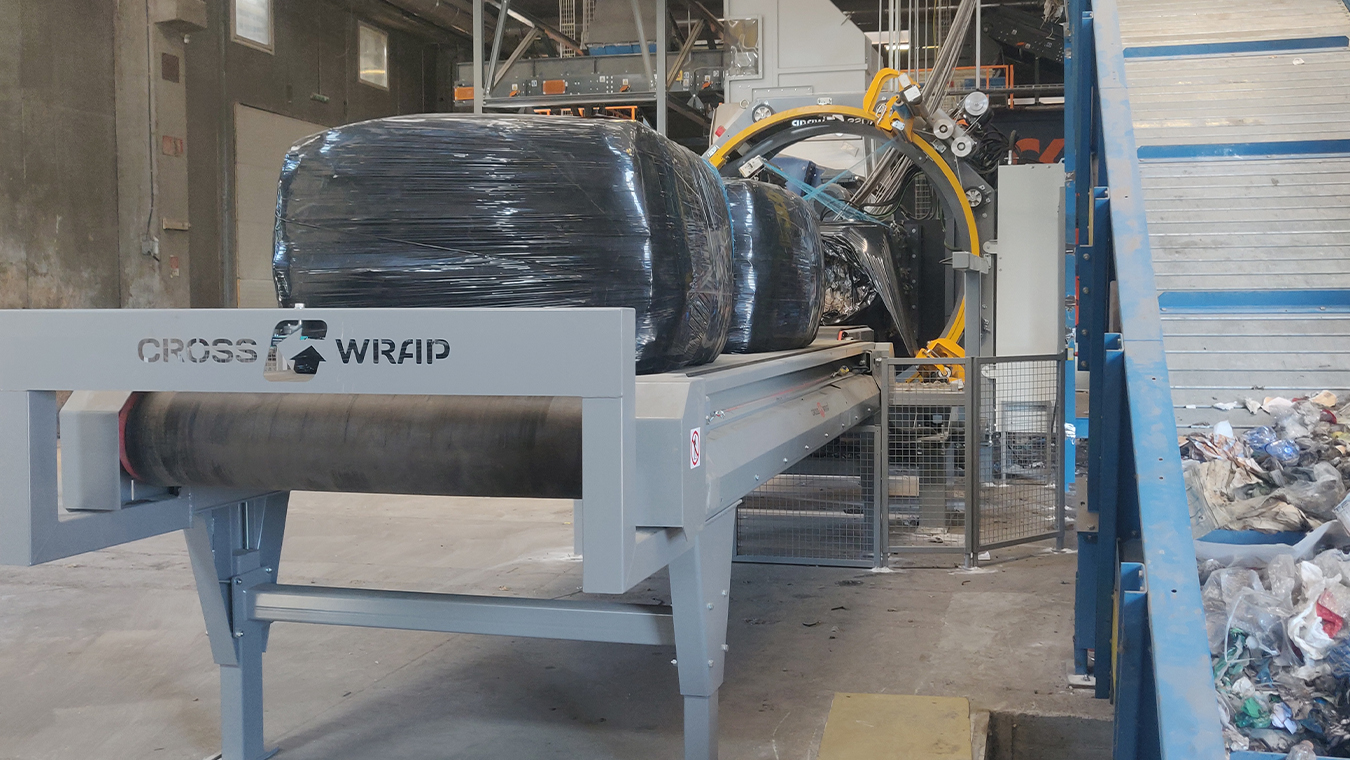
CASE: Papierfabrik improves process safety and effectiveness with CW Dewiring
Papierfabriek Doetinchem in the Netherlands relies on the Cross Wrap Dewiring machine in their highly effective recycling paper production. The mill produces 70 000 metric tonnes of paper from 100% recycled material. The operation runs 24/7 with more than 150 employees.
The production coordinator Ruud Rijks says that CW Dewiring helps to automate recycling and the entire process to develop.
“We saw the improvements for our process straight away when we started to use the CW Dewiring. Now there is less work needed in stock preparation, and the removed bale wires are much easier to store and handle after the Dewiring machine nicely coils them.”
Papierfabrik recommends automatic bale dewiring to any other paper recycling mill.
“The paper recycling industry can benefit from these kinds of modern, high automation material handling solutions when upgrading their processes. For example, the baling wire removal with automatic Dewiring is a step forward when optimising paper recycling and paper mill operations.”
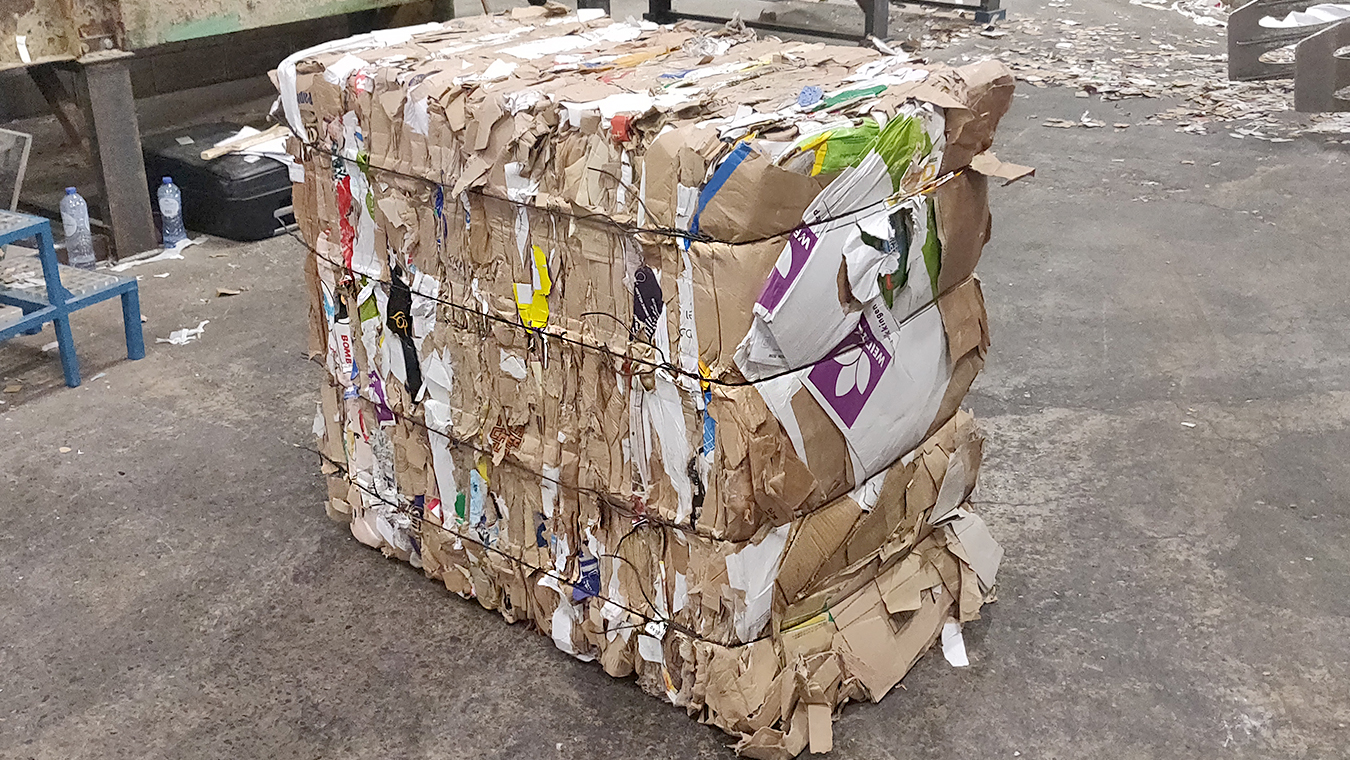
Steady operation flow minimizes downtimes
An efficient paper recycling process naturally requires large investments, modern facilities and agile working methods. This ensures that the material flow is consistent and the production rate is high.
Because your production line needs to be working 24/7 for over 300 days a year, it is reasonable to expect it to operate continuously in every possible condition. It is too big of a risk if your process is dependent on manual feeding of the material while the other segments of the process rely on highly automated phases.
Automated dewiring supports your entire production line as it keeps the feeding of material consistent all the time.
The machine grabs the wires from both sides with patented grippers, and after that, the machine’s front cutters cut the wires. The bale is then conveyed forward, and the device coils the metal wires automatically into a tight bundle.
Also, automatic dewiring reduces the need for pulper maintenance and cleaning. Because a smaller quantity of metal wires end up in the pulper, it means less burden on pulper blades and less pulper run downs.
“Before, we needed to pay to get rid of the uncoiled bale wires, and the pulper emptying was a very labor-intensive operation. Today we get money back from the wire recycling, and the pulper maintenance workload and costs have decreased significantly.”
– Janne Ruoti, The factory operations manager in the Finnish Sonoco Alcore Karhula board mill. Read more.
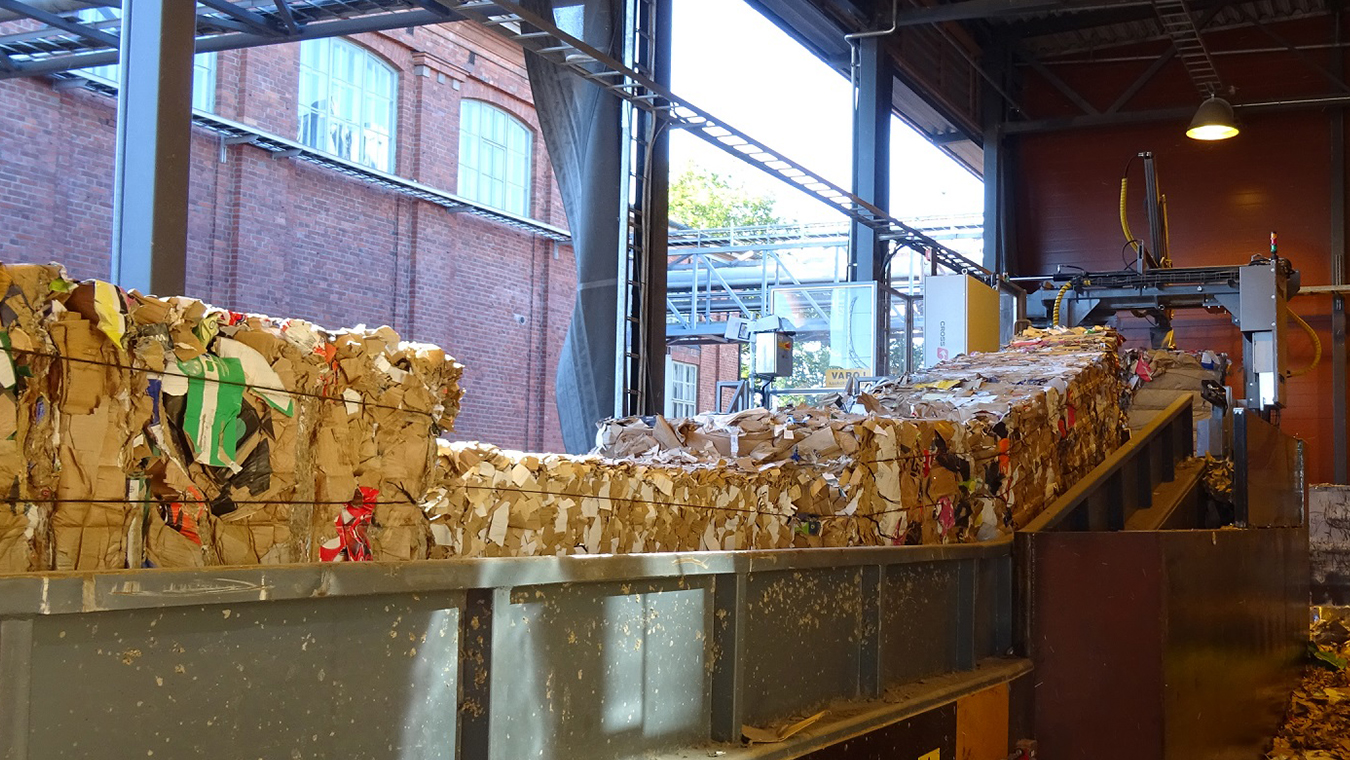
Automatic dewiring saves money, the environment and people in paper recycling
CW Dewiring – highlights at a glance
- Cuts, removes, and coils steel wires from bales before they are moved to the pulper
- Minimizes the need for ragging, landfilling and helps you to take a step towards sustainable zero-landfill practices
- Coiled wires can be easily recycled as metal
- Automatic wire removal creates less need for pulper cleaning and maintenance as the wires don’t end up in the pulper
- Fully automated and smart operation
- It is possible to operate and update the machine remotely
Learn more about the Cross Wrap Dewiring machine.
Read next: Circular economy is part of Cross Wrap operations